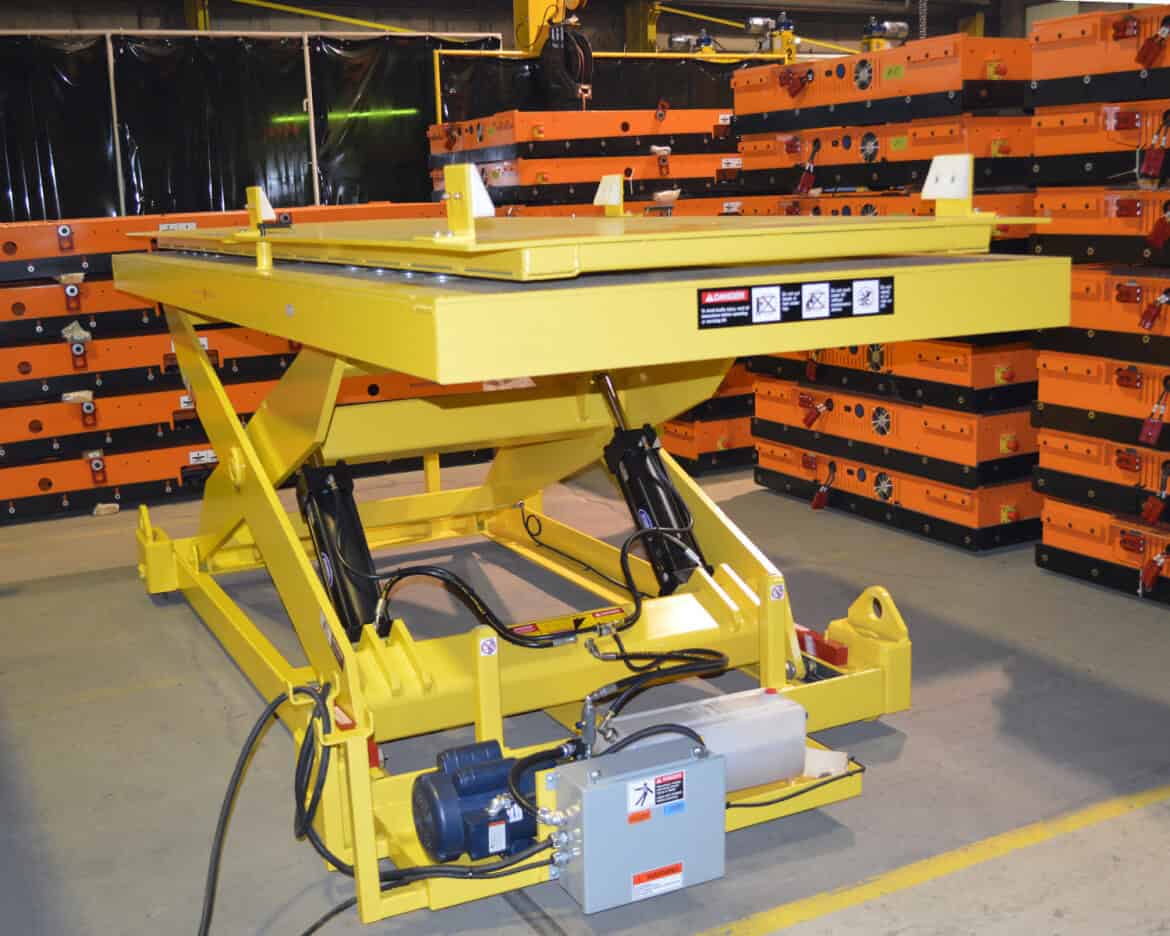
Understanding Hydraulic Scissor Lifts
Understanding the mechanics of hydraulic scissor lifts is crucial for safe operation. These lifts, which are platforms that move up and down using a scissor-like system powered by hydraulic fluid or air, are commonly used in assembly facilities and for maintenance tasks. A clear understanding of how these lifts work can help operators prevent potential accidents.
To use hydraulic scissor lifts safely, operators must have a comprehensive understanding of how they work. Each lift can change height within a specific range and comes in different sizes and lifting capacity limits. Operators need to be familiar with each lift’s controls, safety features, and limits. This knowledge empowers them to work safely and efficiently, instilling a sense of competence and control.
The Basics of Hydraulic Scissor Lift Operation
The heart of a hydraulic scissor lift is the hydraulic system. This closed-loop system consists of a reservoir, pump, valves, and cylinders. It works by sending power through hydraulic fluid, which cannot be compressed. The hydraulic pump pressurizes the fluid when the operator pushes the lift’s controls.
This pressurized fluid flows through the valves and into the lift cylinders. The pressure pushes the piston in the cylinder to move out. This action splits the arms of the scissor mechanism apart, lifting the platform. When the operator wants to lower the lift, a different valve lets the pressure out of the cylinders, and gravity takes over.
As the pressure goes down, the weight of the platform or gravity pulls the cylinder piston back. This brings the scissor arms closer, lowering the platform. Knowing these hydraulic basics is important for operators. It helps them understand how the lift works and why keeping the hydraulic system working is vital.
Key Components and Their Functions
Several important parts work together to make a hydraulic scissor lift operate safely and effectively. The power source, which can be an electric motor or a gas engine, drives the hydraulic pump. This pump pulls hydraulic fluid from the tank and sends it under pressure to other parts of the system.
Control valves direct the flow of pressurized fluid to the right cylinders to raise or lower the lift. These valves also control the flow rate, affecting how fast the lift moves. Safety features like emergency stop buttons, limit switches, and pressure relief valves are built into the machine to avoid accidents and keep operators safe.
Operators must understand how each part works and should regularly inspect these parts visually. By spotting potential issues early and reporting them, operators can help maintain a safe working environment.
Safety Protocols for Hydraulic Scissor Lift Operation
Operators need detailed training to learn about the machinery, how it works, and its safety features. Training sessions are available from Handling Specialty. Understanding the manufacturer’s instructions and limits is very important to help avoid accidents and keep the work area safe.
It is also important to inspect the lift’s parts before every use. This includes checking the hydraulic system, the platform’s condition, and the safety devices. Using a pre-operation checklist can help operators check the lift’s safety effectively. Before starting any work, they should always look for potential hazards, like uneven ground or things above that could cause issues, to keep risks low.
Importance of Regular Safety Inspections
Regular safety inspections play a crucial role in accident prevention. These checks, which are designed to identify and fix safety issues before they become major problems, are a key part of maintaining a safe work environment. Ignoring these inspections can lead to accidents, injuries, and expensive repairs.
Operators should perform regular maintenance checks. This includes inspecting the lift’s parts. For example, check the hydraulic system for leaks, the hoses for wear and tear, and the platform for damage or instability. Their diligence in these checks, along with inspecting safety devices such as emergency stop buttons, limit switches, and guardrails, demonstrates their commitment to safety.
Operators play a significant role in preventing accidents by following strict safety standards and including these routine inspections in their work. Their proactive approach and adherence to safety standards contribute to a well-maintained hydraulic scissor lift, which is vital for worker safety and project completion.
Implementing a Comprehensive Safety Training Program
A comprehensive safety training program is key to preventing accidents when using hydraulic scissor lifts. Employers should invest in thorough training that meets or exceeds Occupational Safety and Health Administration (OSHA) standards. This training, which should cover both theory and hands-on practice, is crucial for maintaining a safe work environment.
Good training programs should teach more than just how to operate the lifts. They must also focus on spotting and avoiding hazards. Operators must know the risks of using these lifts, such as falling from heights, tipping over, crushing hazards, or getting electrocuted. Giving them the right knowledge and skills to spot and reduce these risks is crucial for a safe work culture.
Also, training shouldn’t happen just once. It should be an ongoing effort. Regular refresher courses will help remind everyone of safe practices, share new safety guidelines, and handle operators’ worries. By investing in a thorough safety training program, companies can make their work environment safer for employees and follow industry standards.
Common Mistakes in Operating Hydraulic Scissor Lifts
Even with safety measures and training, operators can still make mistakes when using hydraulic scissor lifts. This often happens because they become complacent or unaware. These mistakes can put safety at risk and could lead to serious accidents. It is important to recognize these common mistakes to create a safer workplace and reduce risks.
One frequent error is not doing pre-operation checks or hurrying through them, which can create unsafe situations. Additionally, operators might not see how important it is to be on level ground and properly stabilize the lift. If the scissor lift is not lagged to the factory floor, this can raise the chance of tip-overs. This section will look at five common mistakes operators make and share ways to avoid them.
Overlooking Pre-Operation Checks
One of the most common mistakes with hydraulic scissor lifts is not performing pre-operation checks. These checks are critical. They help find potential hazards and ensure the lift works properly before use. Skipping this step can raise the risk of accidents and put workers and the product in danger.
Pre-operation checks mean checking the work area for dangers like uneven ground, overhead objects, or possible collisions with other machinery. Operators should also check the lift itself. They need to check the hydraulic system for leaks or damage. Safety features like an emergency stop button, limit switches, and guardrails are also important.
Taking time for these checks can help keep the work environment safe. Following a strict inspection plan helps operators reduce risks. They can then focus on their jobs, knowing they are using a safe and working lift.
Ignoring Load Capacity Limits
Each hydraulic scissor lift is designed to handle a specific maximum load limit for how much weight it can handle safely. This limit must never be exceeded. You can find this limit in the manufacturer’s manual and often on the lift itself. It’s very important to follow this limit. Doing so helps keep the lift stable and prevents damage to the lift that can lead to accidents. Ignoring these limits can significantly increase safety risks for the operators and those around them.
Overloading a scissor lift can cause many dangerous issues. Extra weight can make the lift unstable, making it more likely to tip over, especially when working at great heights. The hydraulic system can also become strained, leading to parts failures and a sudden loss of control. Just like boom lifts, scissor lifts should only be used within their load limits.
Always check the total weight of people, tools, and materials on the platform. Be careful and spread the weight out evenly. This helps keep the center of gravity balanced. Remember, going over the load limit breaks safety regulations and endangers lives.
Neglecting Proper Positioning and Stabilization
Before using a hydraulic scissor lift, operators should check that it is on strong and flat ground. If the ground is uneven, it can cause the lift to feel unstable and may lead to tip-overs, especially as you lift the platform. Not making sure the lift is stable is a common error that can result in serious problems.
Most scissor lifts have extensions or stabilizers or are bolted to the factory floor to create a broader base and improve support. Operators must use these extensions according to company rules before lifting the platform. Forgetting this can throw off the lift’s balance, particularly on uneven or sloped ground.
Stability is even more important when working at the highest point or reaching further with the lift. The added height can make the lift more likely to tip over. Operators must focus on stability by using a strong base and deploying the outriggers to keep a safe working environment.
Skipping Routine Maintenance Checks
Regular maintenance is essential for the safe and efficient operation of machinery, including hydraulic scissor lifts. If routine inspections are skipped, performance can decline, and parts may wear out, leading to expensive repairs or accidents.
Like taking care of any vehicle, these lifts need regular checks, oiling, and replacing worn parts. Following the maintenance schedule in the manufacturer’s manual is key. Operators should know how to spot potential issues like hydraulic fluid leaks, worn hoses, or safety features that don’t work properly.
By investing in regular maintenance, businesses can extend the life of their hydraulic scissor lifts. This also helps create a safer work environment for operators and products. It’s a smart plan that saves time and money in the long run.
Proper Maintenance Practices for Hydraulic Scissor Lifts
Having a good maintenance routine can help avoid expensive downtime and help the equipment work its best. This means regularly checking the lifts, cleaning them, oiling moving parts, and changing out worn parts on time.
By following the manufacturer’s maintenance schedule and quickly fixing any potential issues, businesses can make their scissor lifts last much longer. This is a smart investment that leads to better productivity, lower repair costs, and a safer place to work.
Regular Cleaning and Lubrication
Keeping a hydraulic scissor lift clean and well-oiled helps the lift work smoothly and prevents important components from wearing out too soon. Regular cleaning removes dirt and harmful materials from the outside and inside of the lift.
Operators should clean the platform, guardrails, and base of the lift often, using the cleaning products recommended by the manufacturer. It is especially important to clean under the lift, where dirt can build up and impact the lift’s mechanical parts.
Lubrication is essential, too. It helps reduce friction between moving parts, reducing wear and tear. According to the manufacturer’s guidelines, you should put the right lubricant on moving surfaces. Regular lubrication keeps the lift running smoothly and protects it from rust and corrosion, helping the machinery last longer.
Hydraulic System Care and Inspection
The hydraulic system is vital for a scissor lift. Proper care is key for safe and reliable use. Checking and maintaining the hydraulic parts regularly can avoid expensive downtime, help the lift last longer, and, most importantly, prevent accidents.
Check the hydraulic system for leaks. Pay special attention to hoses, fittings, and cylinders. Look for signs of hose damage, like cracks, bulges, or scratches. Any leak, even a small one, should be immediately fixed by a qualified technician. This can prevent more damage or serious failures.
Also, check the hydraulic fluid level of your hydraulic scissor lift and its condition often. Low fluid levels can lower performance and make parts wear out faster. The fluid’s color can show if there are problems. If it looks dark, cloudy, or has debris, it may be dirty and must be replaced. Check the manufacturer’s guidelines for the right fluid type and viscosity. Keeping the hydraulic system in good shape is very important for the efficient operation of the lift.
Addressing Wear and Tear Proactively
Even if you keep up with maintenance, wear and tear will still happen with any machinery, like hydraulic scissor lifts. It’s important to deal with signs of aging right away. This can help avoid big breakdowns, reduce downtime, and keep operators safe in the long run. If you ignore these signals, it can lead to expensive repairs or even serious failures.
Operators need to pay attention and let someone know if they hear strange noises, feel vibrations, or notice any changes in how the lift works. Regular checks should look closely at all parts, like the platform, scissor arms, hydraulic hoses, safety features, and electrical connections. Watch for any wear, damage, or corrosion.
By fixing these problems quickly, businesses can prevent small issues from turning into big problems. This proactive step saves time and money and can also help keep people safe. Changing worn parts before they break can prevent accidents and help maintain a safe and effective workplace.
Enhancing Operator Training Programs
Operators play a key role in ensuring safety on job sites. Improving their training programs is very important. It helps them gain the knowledge and skills they need to use hydraulic scissor lifts safely. Good training includes more than just how to use the equipment. It also covers spotting dangers, reducing risks, and handling emergencies.
Training is an ongoing effort that requires regular updates, refresher courses, and hands-on practice. When companies invest in training skilled and safety-focused operators, they help reduce accidents. This, in turn, keeps productivity up and builds a strong safety culture in the workplace.
Incorporating Hands-On Training Sessions
With help from experienced instructors, trainees can practice key skills. They will learn to operate the lift at various heights and correctly use safety features like emergency stop buttons. Hands-on training also helps operators get used to the lift’s controls, understand its limits, and practice emergency steps. This includes lowering the platform manually if there is a power outage.
Training programs connect theory and practice by adding practical exercises. This gives operators the skills and confidence they need to handle real work situations safely, lowering the chance of accidents and building a stronger safety culture within the organization.
Conclusion
In conclusion, using hydraulic scissor lifts requires a strong understanding of safety rules. Avoiding common mistakes, like skipping pre-operation checks and neglecting maintenance, is integral to preventing accidents. Regular safety inspections, training programs, and proper maintenance practices help keep hydraulic scissor lifts safe and efficient. When operators focus on safety and maintenance, they can reduce risks and extend the life of the equipment. This creates a safe environment for everyone. Remember, safety is paramount when working with hydraulic scissor lifts. It helps prevent accidents and keeps operations running smoothly.
Frequently Asked Questions
What are the most common hydraulic scissor lift injuries?
Common injuries can result from falls, traps, crushing, and hits caused by products falling over. Fatalities may also occur due to items tipping over, electrocutions, or workers being crushed by falling objects. It’s essential to be careful and check the work area well to reduce these safety risks.
How often should hydraulic scissor lifts undergo maintenance?
Regular maintenance is very important. Follow the manufacturer’s advice for maintenance schedules. Daily checks of safety features should be part of your routine. Depending on how much you use the equipment, you may need deeper checks and repair work on hydraulic components every week, month, or year. This will help keep everything running efficiently.