Elevate Efficiency with Advanced Material Handling Maintenance
Proper material handling solutions are important for your assembly, manufacturing, and MRO facilities. Companies are focusing more on complete maintenance solutions to perform well and keep up. This blog explains how material handling maintenance is evolving. It highlights key factors to consider and best practices that can help your business achieve operational excellence..
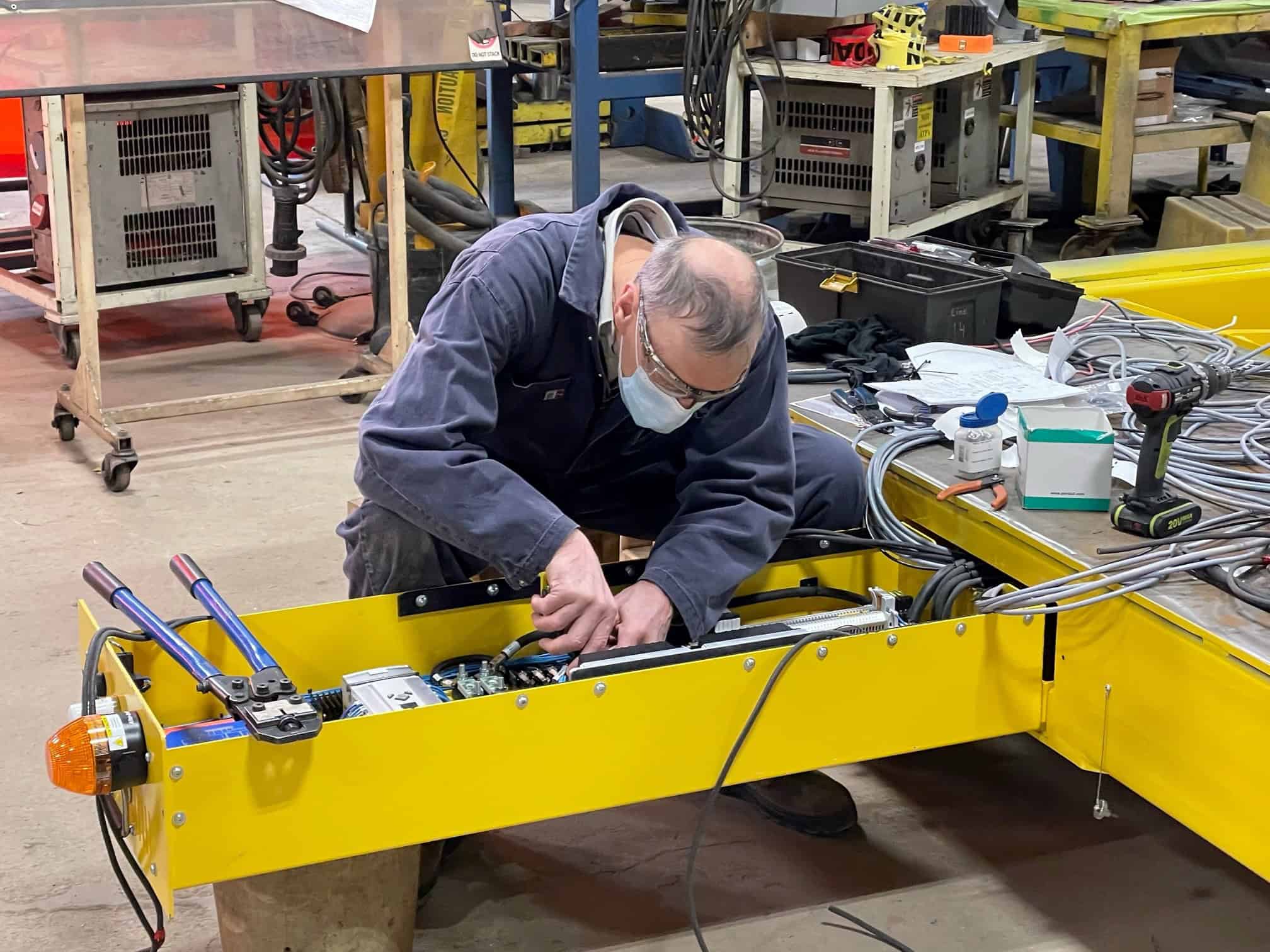
The Evolution of Material Handling Maintenance
Gone are the days of waiting for problems to arise. Today, businesses are embracing a proactive approach, catching issues before they escalate. This not only reduces downtime but also extends the lifespan of equipment, providing a sense of reassurance and confidence in your maintenance strategy.
This change is due to new technology and increased automation. It also comes from understanding how reliable equipment suppliers help business performance. These suppliers play a crucial role in providing high-quality, durable equipment and offering valuable maintenance advice. Let’s examine some key advancements shaping the future of material handling maintenance.
The Shift Towards Automation and Its Impact
Automation and predictive maintenance tools are changing how businesses handle equipment data. Companies now use sensors, analyze data, and apply machine learning. This allows them to see how their machines operate in real-time. They can also predict issues and enhance their maintenance plans.
Predictive maintenance tools provide valuable information on how well equipment works. This information helps companies shift from regular maintenance to maintenance based on current conditions, greatly reducing unplanned downtime. It also helps use resources more effectively and increases the lifespan of key machines.
Still, moving towards automation brings new issues. As companies switch to more complex systems, they may face challenges such as system integration, data security, and the need for skilled technicians who can manage these new technologies.

Integrating IoT for Predictive Maintenance Strategies
The Industrial Internet of Things (IIoT) is a game-changer in predictive maintenance. By connecting material handling equipment to a central network, businesses can access real-time information on factors like temperature, vibration, and energy consumption, keeping them informed and up-to-date.
They examine this data to find patterns or problems that could cause equipment failure. This information is also fed to the OEM, who can then recommend maintenance before a catastrophic event shuts down the equipment. When they spot these issues early, businesses can plan maintenance in advance, which helps them avoid interruptions in their work. For instance, if a personnel lift starts to vibrate oddly, the maintenance teams can be alerted to identify and fix the problem before it worsens.
IIoT systems allow people to check equipment remotely, enabling greater cooperation between maintenance teams and equipment makers. This allows them to make better decisions and improve their maintenance work.
Key Components of an Effective Maintenance Plan
An effective maintenance plan for material handling requires more than just technology. It needs to consider every part of the equipment’s life. Here are some essential things to include:
You need to check things regularly and perform maintenance before problems arise. Good communication methods are also important. Businesses can lower downtime and create a safer work environment by fixing problems before they happen and looking after equipment.

Regular Inspections and Real-Time Monitoring
Planned Maintenance is essential for an effective material handling maintenance program. These routine inspections help find wear and tear. They also show lubrication needs and other potential issues before they become more significant problems.
Real-time monitoring with sensors and data improves this process greatly. When businesses consistently monitor equipment performance, they can immediately notice unusual signs. This helps them take quick action to prevent safety issues and unplanned downtime. For instance, if a motor’s temperature suddenly rises, it may mean a conveyor belt is overloaded. This shows that acting fast is necessary to avoid damage or accidents.
This proactive approach helps cut downtime, extend the life of equipment, and create a safer work environment for everyone.
Training Staff on New Technologies
Investing in proper training for your staff is as important as buying new technology. Good training helps employees use and care for the latest equipment safely and efficiently. This way, you can get the most benefit from your investment. This is even truer today since many businesses are using more automation and robots.
Training should include how to use new technology and basic maintenance tips. This includes lubrication, safety rules, and how to fix minor problems. When you create training programs, remember these important points:
- Make it specific to each role. Training should match different skill levels. New employees might need basic training, while experienced workers might need special lessons on advanced features.
- Include hands-on experience: Practical exercises and simulations help workers practice what they’ve learned in a safe way, building their confidence and skills.
- Offering ongoing learning opportunities is crucial in a rapidly evolving technological landscape. By providing employees with opportunities for refresher courses, webinars, and vendor certifications, businesses empower their workforce to stay updated on new advancements, fostering a sense of preparedness and empowerment.

Overcoming Common Maintenance Challenges
Even when we try our best, maintenance problems can still occur. Understanding common issues such as equipment breakdowns, safety hazards, and unexpected repair costs can help businesses prepare and plan well.
Two main issues in material handling are downtime and understanding whether to repair or replace items. A proactive approach can help you tackle these problems effectively.
Addressing Downtime Through Proactive Measures
Downtime can lead to lost productivity, missed deadlines, and lost money, so it is important to keep it low. While some downtime is necessary for maintenance, a proactive approach can reduce its frequency and impact.
By creating preventive maintenance schedules, you ensure that equipment receives care when it needs it, lowering the chance of sudden failures. This process includes tasks such as lubrication, inspections, and part replacements. A computerized maintenance management system (CMMS) can help keep track of maintenance tasks and plan downtime. It can also manage inventory, improving maintenance work.
Having a clean and organized workspace can help reduce the risk of accidents and damage to equipment.
Cost-Effective Repairs vs. Replacement Decisions
When equipment stops working, businesses must decide whether to fix it or buy new equipment. Making the right choice to save money requires thoughtful consideration. At times, repairing might seem less expensive in the beginning.
If the equipment is old or frequently breaks, it might be wise to replace it. You should consider repair costs, the age of the equipment, how easy parts are to find, and new technology. These factors can help you make better decisions.
Talking to equipment makers or skilled maintenance providers can provide valuable advice. They can help you find the best and most affordable solution for your needs.

Conclusion
In conclusion, the way we take care of material handling equipment is changing. We are now using automation and IIoT to work better and faster. Predictive maintenance is becoming critical to take care of equipment before problems happen. It’s essential to use real-time monitoring and train staff on new technology for a strong maintenance plan. We must handle issues like downtime smartly and take proactive steps. To be successful in material handling maintenance, businesses must keep up with trends and technologies. A proactive approach to maintenance is key for better efficiency and saving money.
Frequently Asked Questions
What Are the Latest Trends in Material Handling Maintenance?
The latest trends in material handling and maintenance solutions focus on using IIoT and data analysis to predict maintenance needs. Tasks are also automated. Additionally, tools that use AI for diagnostics and optimization are gaining attention.
How Does Automation Affect the Maintenance of Material Handling Equipment?
Automation requires specific training for maintenance workers and regular software updates. Safety is also being prioritized to protect against risks.
Can Predictive Maintenance Extend the Life of Material Handling Equipment?
By spotting problems early, businesses can fix them before they become serious and make better-planned maintenance arrangements. This helps increase the lifespan of important material handling equipment. Predictive maintenance supports preventive maintenance by analyzing real-time data.
What Training Does Staff Need to Operate New Material Handling Technologies?
Staff needs complete training on how to use new technologies safely and effectively. This training should include control systems, software interfaces, troubleshooting, and following safety standards.
How Can OEMs Stay Ahead in Material Handling Maintenance?
Original Equipment Manufacturers can improve by using automation and predictive maintenance strategies. They should also invest in worker training. Partnering with reliable OEM maintenance service providers is a good idea. These providers know their specific needs and the changing demands of different industries.